Retractable Device Could Make Vehicle Camouflage Easier
Retractable Device Could Make Vehicle Camouflage Easier
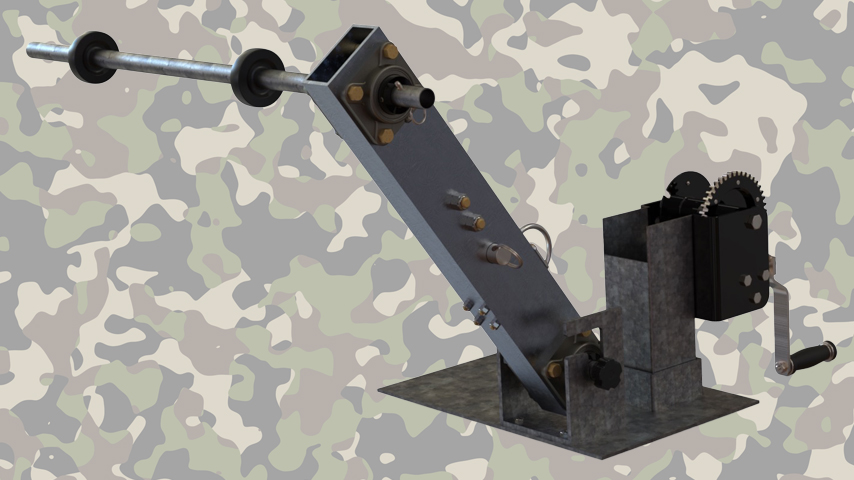
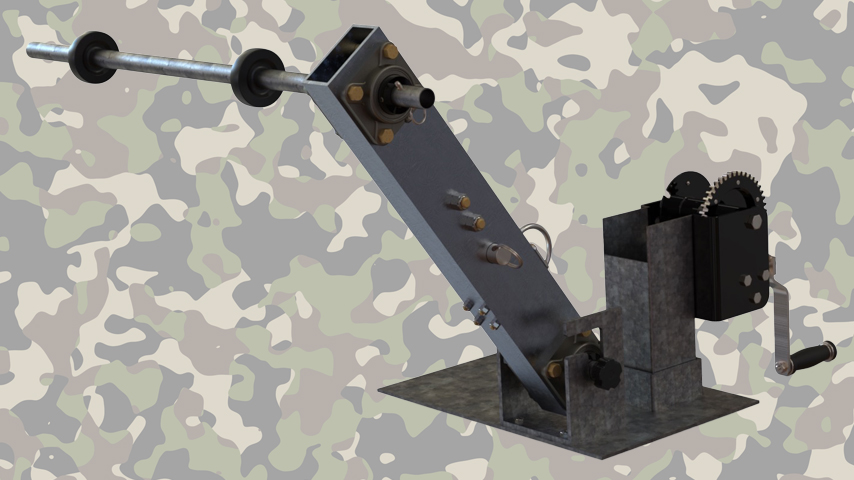
A class project at the University of Florida has transformed into a fast, safe way for soldiers to camouflage vehicles on the battlefield.
While in combat, soldiers take every precaution to conceal themselves and their vehicles from the enemy. Currently, Army troops use camouflage netting to cloak vehicles, which works to hide the vehicle type and obscure its position. But it takes several soldiers nearly an hour to deploy the netting, and if they happen to be spotted, removing the netting is a slow process that puts troops at risk.
“If the soldiers come under fire, they currently have to jump out of the truck and wander around in the field to grab the corners of the netting, fold it, and toss it in the back of the truck,” explained Matthew J. Traum, instructional associate professor for the Department of Mechanical and Aerospace Engineering at the University of Florida.
The Army often engages industry professionals, and in this case, academic institutions, to improve the quality and functionality of all kinds of military equipment. Working with the Georgia Institute of Technology and the Civil-Military Innovation Institute, Traum secured this project for his students in 2023. He organized three consecutive capstone semesters to advance the project from concept to prototype in one year, which Traum said is a remarkable timeline compared to the Army’s conventional product development cycle.
The student capstone teams addressed three main customer needs: The netting deployment mechanism should be retractable, it should take up minimal space in the vehicle, and it needs to withstand harsh environments. Through brainstorming and down-selection processes, the students determined the best system to meet these needs was a hand-cranked spooling mechanism like a firetruck’s hose.
Discover the Benefits of ASME Membership
So, they designed a system to thread the netting together using paracord, making it easier to deploy and retract systematically. However, the students discovered early on that their main challenge would be working with the camouflage netting, which weighs more than 100 pounds.
“The first couple iterations of the design would get jammed in the device, and it would take a while to unjam it,” said Isaiah King, an engineering student from the spring 2024 capstone class. “So, we had to try several configurations and conduct a lot of testing, which took dragging the 100-pound camouflage netting out and starting over.”
But the netting's size and weight also challenged the students to work with heavy-duty materials to build the mechanism. It takes significant force to retract the netting, which means the hand crank had to be durable enough to withstand multiple deployments before being serviced. The Army requested that the camo deployer be manual because soldiers can’t always fix electrical components in the field if they malfunction.
The box that deploys and retracts the netting fits compactly in the back of the truck. It is mounted to an elevated chassis, giving the soldiers additional storage space.
“This is a great example of design synergy,” said Traum. “It not only has more effective deployment and retraction functionality, but it’s more efficient in its use of space than the current camo net.”
Now that the prototype has been finalized, the device will be taken to an Army proving ground where it will be tested in simulated warfare conditions. From there, soldiers using the camo deployer will generate new observations and requirements to inform the next phase of the university-military design collaboration, which Traum anticipates will occur as a fourth capstone project in the series.
You Might Also Enjoy: AI Helps Soldiers Bark Orders Telepathically to Robot Dogs
“We hope the students will get another crack at it,” Traum said. “This will be the final phase, so those future students will be able to see what it takes to push a new product into full-scale production.”
Capstone projects like this give engineering students an opportunity to work on real-world designs fostering the technical rigor it takes to move a project along. They also get to work directly with external clients, receiving their feedback along the way.
“This class was rewarding because textbooks and lectures can only teach you so much,” King said. “The field of mechanical engineering is so broad, and I never understood exactly where I wanted to go next. So, having the design and implementation experience helped me see what I wanted to do in my career.”
Cassandra Kelly is a technology writer in Columbus, Ohio.
“If the soldiers come under fire, they currently have to jump out of the truck and wander around in the field to grab the corners of the netting, fold it, and toss it in the back of the truck,” explained Matthew J. Traum, instructional associate professor for the Department of Mechanical and Aerospace Engineering at the University of Florida.
The Army often engages industry professionals, and in this case, academic institutions, to improve the quality and functionality of all kinds of military equipment. Working with the Georgia Institute of Technology and the Civil-Military Innovation Institute, Traum secured this project for his students in 2023. He organized three consecutive capstone semesters to advance the project from concept to prototype in one year, which Traum said is a remarkable timeline compared to the Army’s conventional product development cycle.
The student capstone teams addressed three main customer needs: The netting deployment mechanism should be retractable, it should take up minimal space in the vehicle, and it needs to withstand harsh environments. Through brainstorming and down-selection processes, the students determined the best system to meet these needs was a hand-cranked spooling mechanism like a firetruck’s hose.
Discover the Benefits of ASME Membership
So, they designed a system to thread the netting together using paracord, making it easier to deploy and retract systematically. However, the students discovered early on that their main challenge would be working with the camouflage netting, which weighs more than 100 pounds.
“The first couple iterations of the design would get jammed in the device, and it would take a while to unjam it,” said Isaiah King, an engineering student from the spring 2024 capstone class. “So, we had to try several configurations and conduct a lot of testing, which took dragging the 100-pound camouflage netting out and starting over.”
But the netting's size and weight also challenged the students to work with heavy-duty materials to build the mechanism. It takes significant force to retract the netting, which means the hand crank had to be durable enough to withstand multiple deployments before being serviced. The Army requested that the camo deployer be manual because soldiers can’t always fix electrical components in the field if they malfunction.
The box that deploys and retracts the netting fits compactly in the back of the truck. It is mounted to an elevated chassis, giving the soldiers additional storage space.
“This is a great example of design synergy,” said Traum. “It not only has more effective deployment and retraction functionality, but it’s more efficient in its use of space than the current camo net.”
Now that the prototype has been finalized, the device will be taken to an Army proving ground where it will be tested in simulated warfare conditions. From there, soldiers using the camo deployer will generate new observations and requirements to inform the next phase of the university-military design collaboration, which Traum anticipates will occur as a fourth capstone project in the series.
You Might Also Enjoy: AI Helps Soldiers Bark Orders Telepathically to Robot Dogs
“We hope the students will get another crack at it,” Traum said. “This will be the final phase, so those future students will be able to see what it takes to push a new product into full-scale production.”
Capstone projects like this give engineering students an opportunity to work on real-world designs fostering the technical rigor it takes to move a project along. They also get to work directly with external clients, receiving their feedback along the way.
“This class was rewarding because textbooks and lectures can only teach you so much,” King said. “The field of mechanical engineering is so broad, and I never understood exactly where I wanted to go next. So, having the design and implementation experience helped me see what I wanted to do in my career.”
Cassandra Kelly is a technology writer in Columbus, Ohio.
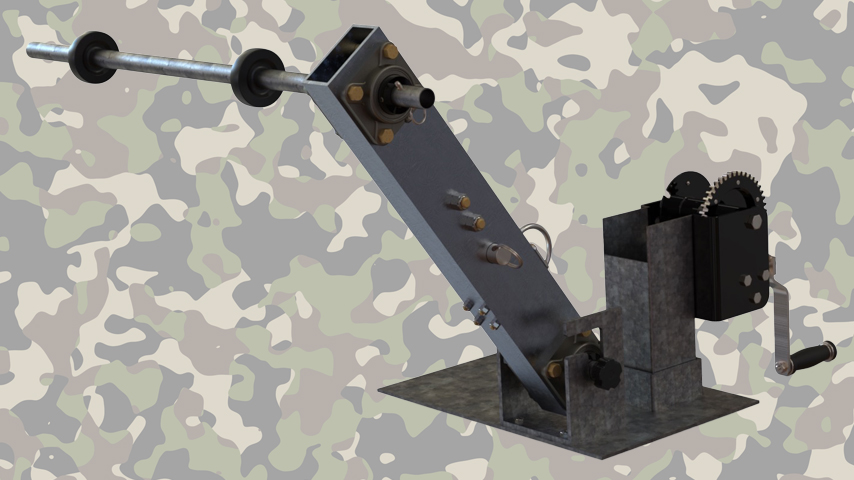
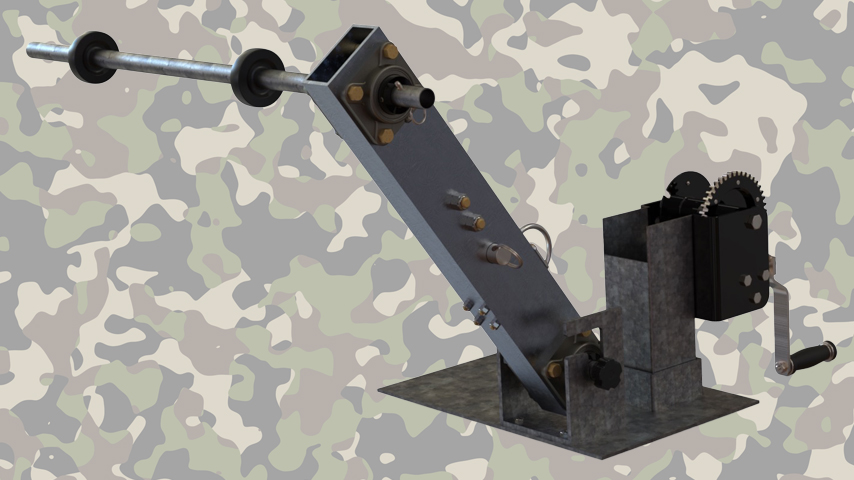